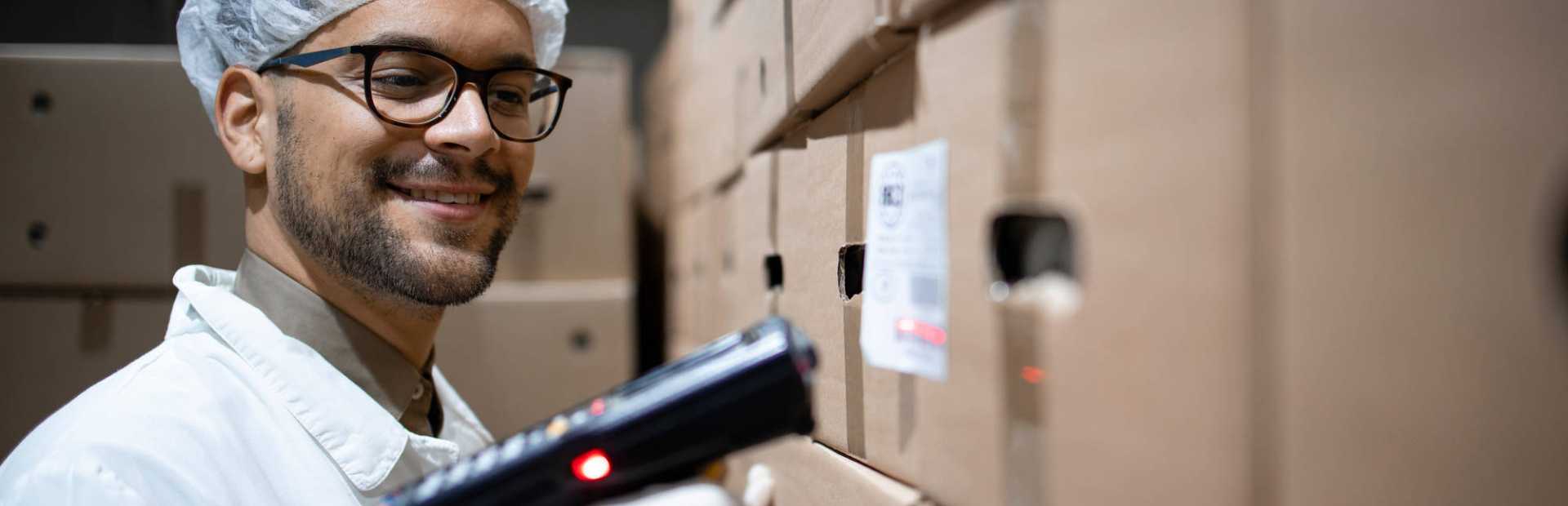
Quality Tools Trainings
Revolutionize Your Quality Performance with Quality Tools Trainings
In the rapidly evolving world of manufacturing and service industries, ensuring quality has become an absolute necessity. But, how can one consistently ensure quality across processes? This is where the significance of quality tools training surfaces. It is essential training that delivers the knowledge and skills needed to understand and effectively deploy quality tools in your work environment.
Why is Quality Tools essential
Quality tools are indispensable instruments deployed in quality management to improve processes, amplify efficiency, and increase overall productivity. With an understanding of how to apply these tools accurately, you can effectively pinpoint the cause of problems, analyze their impacts, and craft durable solutions. This competence leads to reduced errors, enhanced customer satisfaction, and eventually, an increased bottom line.
Our course offerings:
- Lean Six Sigma Training: Master the principles of Lean and Six Sigma methodologies to optimize processes, eliminate waste, and reduce variation.
- Eight Disciplines (8D) in Problem-Solving Training: Gain in-depth knowledge of the 8D process and apply it in your workplace to systematically resolve problems.
- Introduction to Six Sigma Training: Get an overview of the Six Sigma methodology and its application to improve quality.
- Root Cause Analysis Training: Acquire the skills to identify the core of problems to prevent their recurrence.
Key benefits of quality tools training include
- Improved Problem-Solving Abilities: Learn the methodologies like Eight Disciplines (8D) and Lean Six Sigma to identify, analyze, and resolve quality-related issues effectively.
- Enhanced Operational Efficiency: By adopting Six Sigma and Lean principles, streamline your processes, reduce waste, and amplify productivity.
- Compliance with Standards: Master the tools required to maintain compliance with quality standards in your industry.
- Increased Customer Satisfaction: By delivering consistent quality that exceeds customer expectations, boost their loyalty and your reputation.
Target audience
Our training is designed to cater to a diverse range of professionals, including:
- Quality management
- Quality assurance
- Process improvement
- Project management
- Team leaders of manufacturing or service industry
Popular training
Don't just settle for good enough. Elevate your career and your organization to the level of greatness.
Enroll in our quality tools training today to drive continuous improvement, maximize customer satisfaction, and secure your competitive edge.
Frequently Asked Questions (FAQ)
Is Quality Tools Training relevant to my industry?
Quality Tools Training is relevant to various industries, from manufacturing to services, as it encompasses universally applicable techniques such as Lean Six Sigma and Root Cause Analysis. These strategies can optimize processes, reduce waste, and improve overall quality, making the training beneficial across sectors.Can Quality Tools Training improve my career prospects?
Yes, acquiring knowledge and skills in quality management techniques, such as Lean Six Sigma and 8D Problem Solving, can significantly enhance your career prospects. These skills are highly valued by employers in various industries, opening doors to roles in quality assurance, process improvement, and project management.What is the format of the Quality Tools Training course at TÜV Rheinland Academy?
Our Quality Tools Training course is designed to facilitate interactive learning through a blend of theoretical sessions and practical exercises. The course also includes real-life case studies to help you understand the application of various quality tools.Do I need any prior knowledge or experience to enroll in the Quality Tools Training course?
While some background knowledge in quality management can be beneficial, it is not a prerequisite for the Quality Tools Training course. The course is designed to accommodate participants with varying levels of knowledge and experience.Can I apply the skills learned in Quality Tools Training to any process in my organization?
Yes, the techniques and strategies taught in Quality Tools Training, such as Lean Six Sigma and 8D Problem Solving, are universally applicable to various processes. They can be used to improve efficiency, reduce waste, and enhance overall quality in any organizational process.Is the Quality Tools Training at TÜV Rheinland Academy internationally recognized?
Yes, TÜV Rheinland Academy offers Quality Tool Training which is internationally recognized. Check in the training description if the course is a certification course in which you receive upon successful completion of the course a valued certificate across industries globally. If it is not a certification course, you receive a certificate of attendance instead.How does Quality Tools Training help in reducing operational costs?
Quality Tools Training equips you with skills to implement strategies like Lean Six Sigma, which aims at improving process efficiency and reducing waste. This leads to optimized resource utilization and significant reductions in operational costs.What support can I expect from TÜV Rheinland Academy after completing the Quality Tools Training course?
TÜV Rheinland Academy offers ongoing support to our graduates, including access to additional learning resources, opportunities for further training, and assistance with any questions or challenges you may encounter in your quality management journey.
-
Enhancing Quality and Productivity: Mastering DMAIC Methodology for Process Enhancement
-
Lean Six Sigma - Yellow Belt (TÜV)
Optimizing Workplace Efficiency: Unlocking Potential with Lean Six Sigma Strategies -
Lean Six Sigma - Black Belt (TÜV)
Equip the knowledge, tools, and strategies to become a certified Lean Six Sigma Black Belt. -
Integrated Management Systems: QMS and ISMS Internal Auditor
Enhance Your ISMS and QMS Professional Skills and Organizational Impact -
Introduction to Six Sigma
Improve Quality with Six Sigma Methodology -
Root Cause Analysis
A Proven Method for Identifying and Eliminating the Source of Problems -
Eight Disciplines (8D) in Problem Solving
8D Problem Solving: Comprehensive Guide